The evolution of press drills in cushion pillow manufacturing tells the story of how a seemingly straightforward household item has undergone dramatic changes through technological innovation. From early manual creation methods to today’s advanced computerized systems, the journey is nothing short of fascinating.
Historical Context of Cushion Pillow Manufacturing
Cushion pillows date back centuries, their origins rooted in handmade craftsmanship. Initially, artisans would meticulously stuff fabric cases with materials like feathers or animal hair using basic tools such as wooden presses and hand sewing needles. Each pillow was a labor of love, far from mass production yet unmatched in its personalized touch.
Introduction of Basic Press Drills
The Industrial Revolution brought about the nascent stages of standardization in many industries, including textiles. As factories began adopting mechanized processes, the first rudimentary press drills made their debut. Although primitive compared to modern standards, these initial devices significantly impacted productivity and consistency in cushion pillow manufacturing. No longer purely reliant on human hands, cushions produced using press drills displayed uniformity hitherto unseen.
Mechanization and Industrial Revolution
The introduction of steam power marked a pivotal shift from manually operated press drills to more effective mechanized solutions. Steam engines were transformative, exponentially increasing the efficiency of press drills and reducing human labor intensity. Early adopters in the textile industry, often cited in historical case studies, reported substantial gains in output and quality. Factories equipped with steam-powered press drills could churn out higher volumes of cushion pillows without compromising on build integrity.
Technological Advancements in Press Drills
As electricity became widespread, electric press drills replaced their steam-powered predecessors, offering greater control and adaptability. These electric versions heralded unprecedented prospects: adjustable speed settings, programmable operations, and heightened precision revolutionized the production line. Customization reached new heights; manufacturers could now tailor stuffing density and firmness to meet varied consumer preferences.
Modern Press Drill Innovations
Today's press drills have woven computer-aided design (CAD) and automation into their core functionalities, embracing robotics and smart technologies. Modern units particularly excel in minimizing errors and maximizing efficiency. They are capable of intricate tasks, previously deemed impossible, thanks to robotic arms and software-driven accuracy. This increased capability translates into faster turnaround times and an overall boost in manufacturing reliability.
Impact on Quality and Design
The sophisticated nature of contemporary press drills permits designers to push creative boundaries. Intricate patterns, unique shapes, and elaborate stitching are all achievable, powering aesthetic advancements in cushion pillows. This evolution has led to products that are not just decorative but also offer enhanced durability and comfort. Technological progression has unlocked extensive customization options, allowing consumers to personalize aspects such as color schemes, textures, and even ergonomic features tailored to individual health needs.
Sustainability and Environmental Considerations
Environmental consciousness within the textile sector has driven innovations aimed at sustainability. Present-day press drills incorporate eco-friendly materials and energy-efficient processes. Technology facilitates meticulous material use, thereby curtailing waste. Additionally, automated systems have drastically cut down energy consumption, making the manufacturing process greener than ever before.
Future Trends in Press Drill Technology
Looking ahead, the integration of artificial intelligence (AI) and machine learning promises further enhancements. Anticipated improvements include machines capable of self-diagnosing issues and optimizing workflows autonomously. Automation will likely continue to evolve, presenting opportunities for even greater operational efficiencies and cost reductions. The next decade holds much potential for breakthroughs that could once again transform the landscape of cushion pillow manufacturing.
Real-World Applications and Success Stories
Numerous companies exemplify the successful application of cutting-edge press drill technology. For instance, leading enterprises in the home furnishings market attribute part of their success to adopting multi-functional, high-tech press drills. Testimonials from these manufacturers highlight benefits ranging from augmented productivity to improved end-product quality. Comparing traditional methods against modern techniques reveals stark contrasts, reaffirming the value intrinsic to advanced machinery.
Key Takeaways and Industry Insights
The journey of press drills in cushion pillow manufacturing showcases remarkable growth sparked by continuous innovation. By leveraging historical insights, manufacturers can glean valuable lessons—key among them, the importance of staying abreast with technological advances. Strategic adoption of emerging trends ensures competitiveness and caters to evolving consumer demands. As the industry stands on the cusp of further change, those who embrace progress will undoubtedly lead the charge towards future excellence.
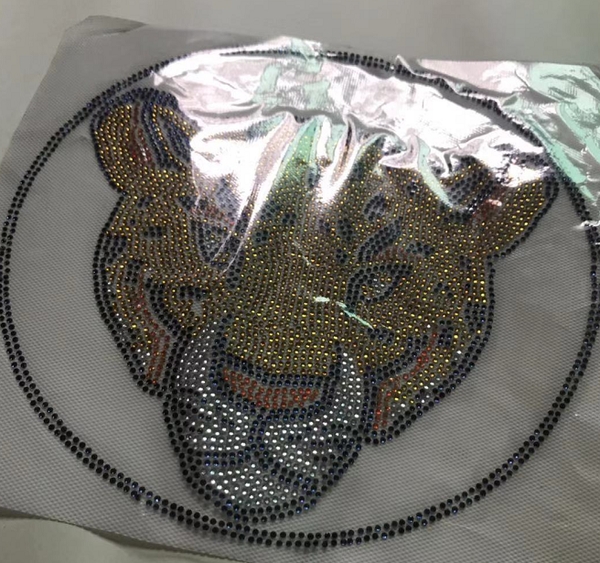